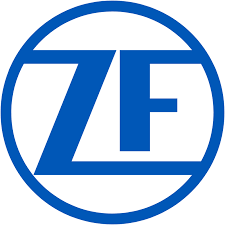
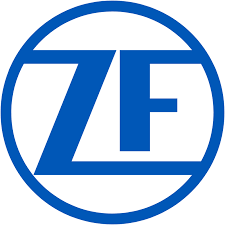
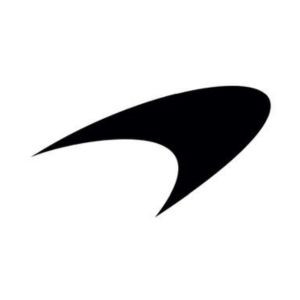
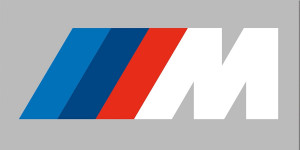
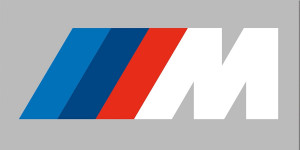
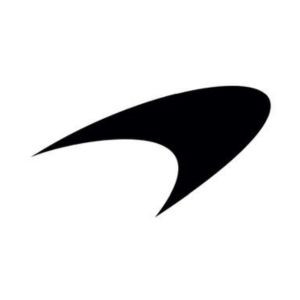
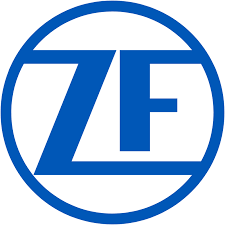
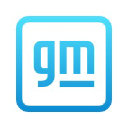
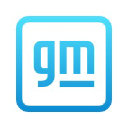
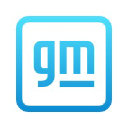
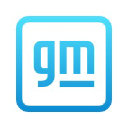
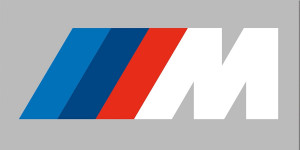
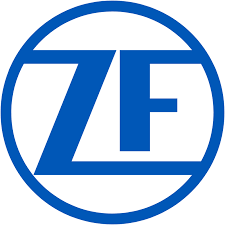
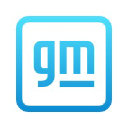
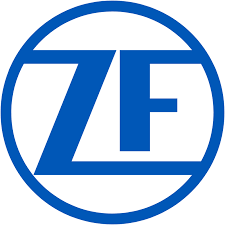
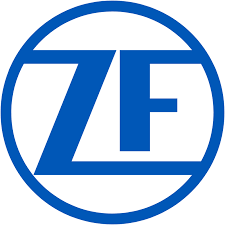
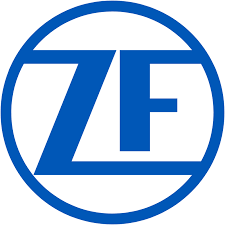
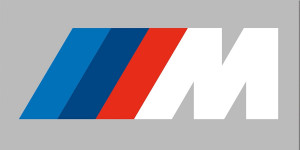
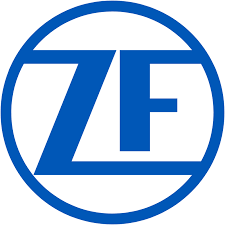
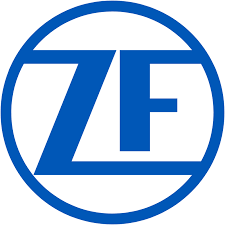
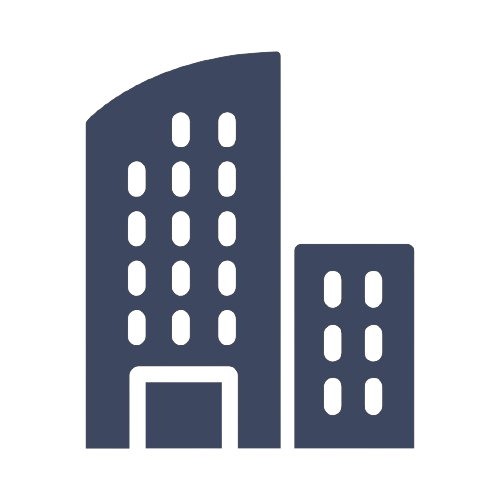
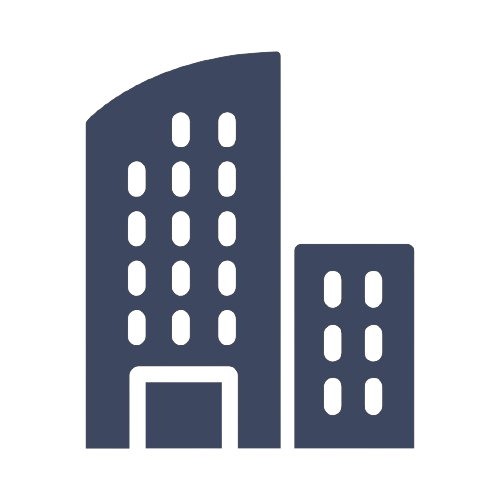
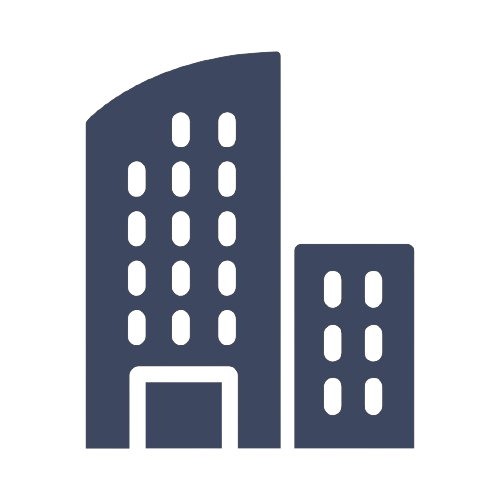
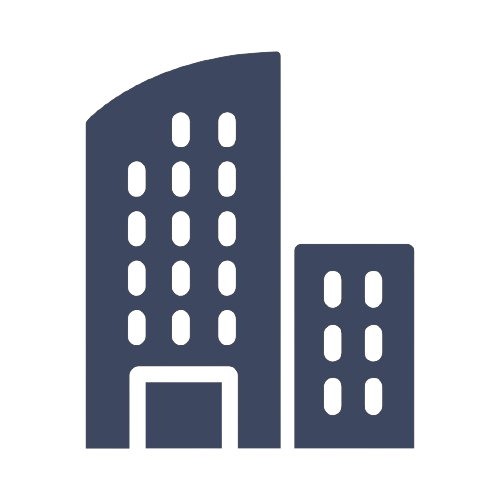
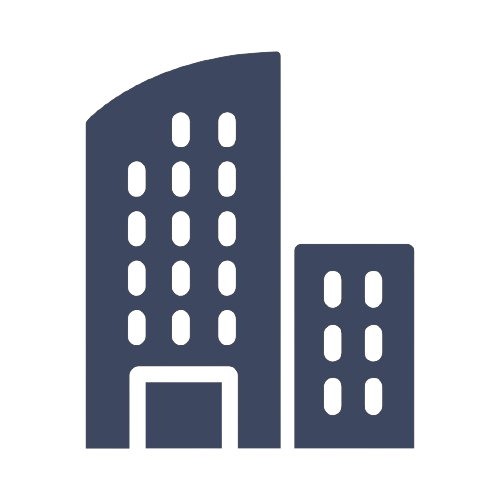
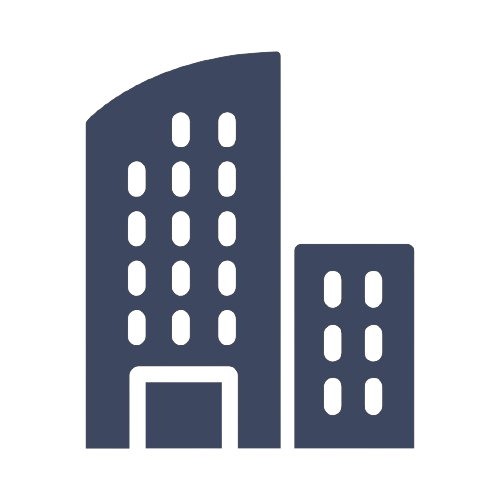
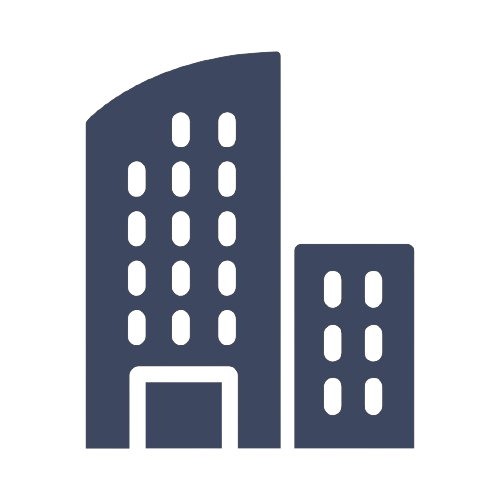
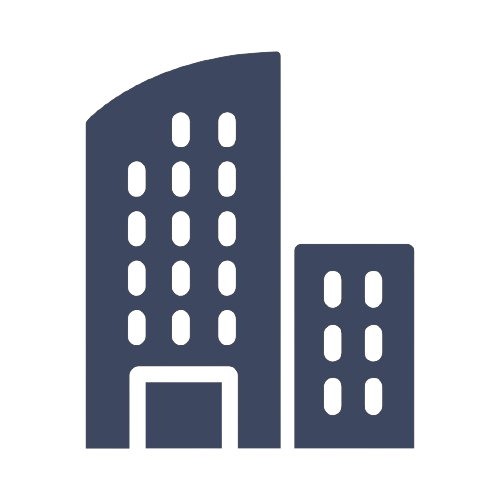
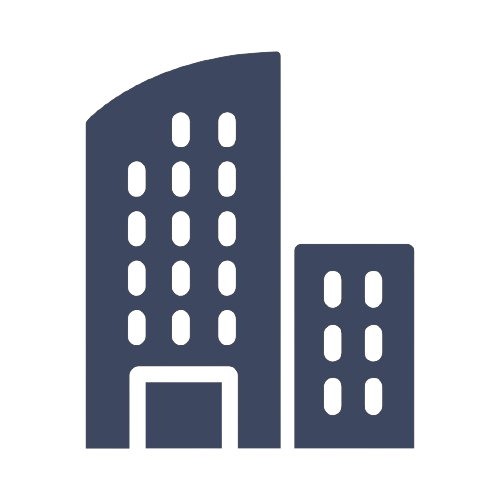
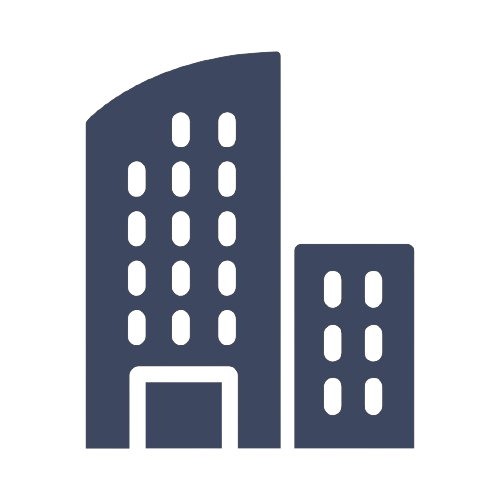
Test Your Formula 1 Career Readiness!
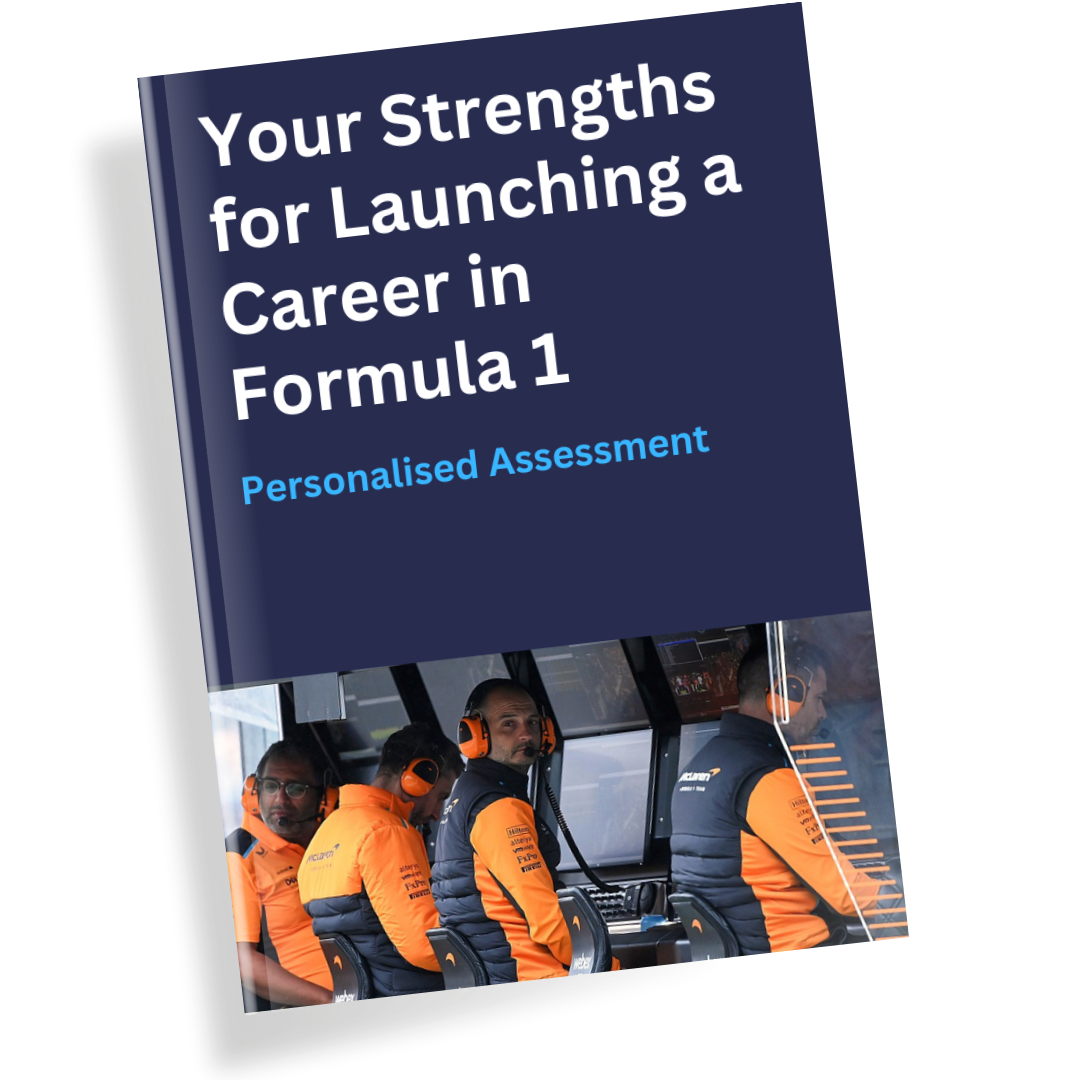
Take the Formula 1 Career Readiness Quiz and find out if you're on track to success. Get a personalised report highlighting your strengths and areas to improve in just 5 minutes!
Take the Quiz NowSoftware engineers in motorsport develop critical applications for race simulation, data analysis, and vehicle control systems. These roles combine advanced programming skills with deep understanding of racing operations.
Software Engineering - Salary Insights
- Graduate/Junior Developer: £35,000 - £50,000 ($44,000 - $63,000)
- Software Engineer: £50,000 - £85,000 ($63,000 - $107,000)
- Senior Software Engineer/Lead: £85,000 - £130,000+ ($107,000 - $164,000+)
Salaries vary based on specialization, racing series, and technical expertise.
Share your salary insights anonymously to help others in the community make informed career decisions.
Software Engineering - Common Specialisations
- Vehicle Systems Developer - ECU and control systems
- Simulation Software Engineer - Race simulation tools
- Data Analysis Developer - Telemetry analysis systems
- UI/UX Developer - Engineering software interfaces
- DevOps Engineer - Development Infrastructure
- Real-Time Systems Developer - Live data processing
Software Engineering - Typical Requirements
- Computer Science degree or equivalent
- Strong programming skills (C++, Python, C#)
- Real-time systems experience
- Software architecture knowledge
- Understanding of automotive systems
- Experience with data visualization
- Version control expertise
Software Engineering - Career Development
Common career progression paths include:
- Junior Developer → Software Engineer → Senior Engineer
- Systems Developer → Technical Lead → Software Architecture
- Application Developer → Team Lead → Technical Director
Create job alerts for software engineering positions and be the first to know about new opportunities across Formula 1, NASCAR, IndyCar, and other racing series. Visit our careers hub for useful information and career advice podcasts featuring insights from people on the cutting edge of motorsport.